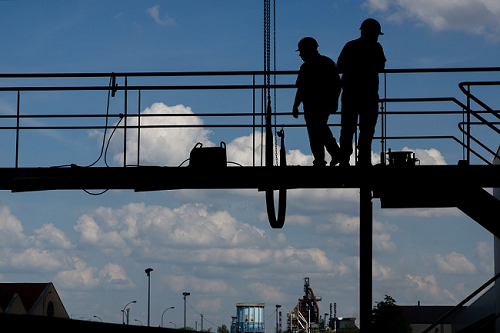
Working at height is one of the main causes of major injuries and fatalities in the construction industry; and common cases include falls from ladders, rooftops and fragile surfaces. HSE defines work at height as "work in any place where, if there were no precautions in place, a person could fall a distance liable to cause personal injury".
To prevent any major or fatal injuries from happening when working at height, it's important that a risk assessment is put in place. A risk assessment is an examination of what in your workplace could cause harm, so you're able to put the right precautions in place to make sure that any work at height is properly planned, supervised and carried out in a safe manner. By law you're required to assess the risks in the workplace so that you can put a plan in place to control the risks.
With that in mind. If you're starting to create a risk assessment, here are some steps you should follow in order to ensure your assessment is accurate and as thorough as possible:
Step 1: Identifying the Potential Hazards
This is arguably one of the most important steps for creating your your risk assessment. When identifying the hazards in your workplace, it's important to think about the activities, processes and/or substances that are used in your workplace that could injure or harm your employees' health. Here are some tips to help you identify potential hazards:
- Observe the workplace.
- Check manufacturers' instructions.
- Look through your accident book.
- Think about long-term hazards to health - for example: exposure to a high level of noise or harmful substances.
- Gather feedback from employees.
The Work at Height Regulations 2005 state that the following need to be considered in your risk assessment:
- The distance and effects of any potential falls.
- The duration and frequency of use of work equipment, and whether the work equipment is appropriate for the work that is about to be performed.
- Does the work equipment allow passage without risks.
- The need for easy and safe evacuation in case of an emergency .
- The working condition and the risks to people where work equipment is to be used.
Step 2: Deciding who may be harmed and how
It's important when conducting a risk assessment that you think about which people are at risk, and how they might be harmed. For each hazard you need make sure it is clear which group of people might be harmed, as this will help you identify the best way of controlling the risks. It's important to make sure you consider every person in the work area:
- Employees.
- Visitors.
- Contractors.
- Maintenance workers.
- Members of the public.
- If you share a workplace with another business, consider how each of your work affects yours, and their workers.
Step 3: Evaluate the Risks
Having identified the potential hazards, you now have to identify the level of the risk and what precautions you need to put in place. You are not expected to eliminate all risks; but you need to make sure you're aware of them, and the things you must do to manage and prevent them. Your risk assessment should only include what you're expected to know - you are not responsible for anticipating unforeseeable risks.
Look at what you're already doing, and what control measures you have in place - and evaluate if it's possible to get rid of the hazard? And if not; how can you control the risks to reduce the chances of it doing any harm.
Some practical steps you should consider when preventing the risks of hazards:
- Issue the correct personal protective equipment.
- Preventing access to the hazards.
- Ensuring that all workers are trained to ensure that they understand the hazards and the precautions to be taken.
- Trying a less risky option.
- Organising work to reduce any exposure to the hazard.
- Providing welfare facilities such as first aid and washing facilities.
Step 4: Record Your Findings
When you're recording your findings it's important that you keep it simple and that it's easy to read. An accurate risk assessment should show the following:
- A proper check has been made.
- You have shown who might be affected.
- You have dealt with the hazards and have taken in account who might of been affected.
- The precautions are sensible and that the remaining risk is low.
- You have involved all your employees during this process.
To prevent any confusion, it's important that you use a new risk assessment sheet for each work place and assessment you complete. You must ensure that you have dated the risk assessment; that you have recorded details of the person who took the assessment, and that you have recorded any action due-dates and completion dates.
Step 5: Review & Update Your Assessment
Workplaces are always changing and bringing in new equipment, substances and procedures that could possibly lead to new hazards. So, it's important that you review what your risk assessments every 6-12 months. It's important to check the following:
- Any significant changes at your workplace?
- Are there any improvements you need to make?
- Have your workers noticed a problem?
- Have you learnt anything from recent accidents?
When working with height it's always important that the correct safety measures are put in place. That's why we supply a comprehensive range of Height Safety Equipment that are designed to ensure the maximum level of protection, while also providing an assuring level of comfort too. To view our range of height safety equipment, please click here.